Dairy Products Industry
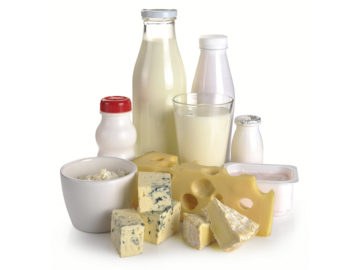
The dairy industry has been meeting consumer demand for more innovative drinks, snacks and milk-like products. They have added popular, high-margin items such as greek yogurt and gourmet cheeses to their portfolios to insulate themselves from swings in the demand for basic milk products.
Food Technology magazine cites that Greek style yogurt and yogurt-based foods account largely for dairy industry demand, representing one-third of dairy products packaged today. Greek yogurts are so popular that it’s not uncommon for suppliers in general to be diversifying in to yogurt based foods - dips, spreads, drinks and soft cheeses etc - for a chance to maximize on its promoting and selling power.
Yogurt and Gourmet Cheese Application
From a packaging perspective, dairy product producers that approach us, commonly express concern over maintaining product safety, reliability, and mitigating the chance of ‘spoilage’. The challenge related to delivering the right product, in the right quantity, just in time and on time is important to any operation. This is particularly true for dairy producers, for whom freshness concerns are paramount. Our dairy customers come to us for solutions to increase speed and deliver line flexibility to help them quickly adapt to product trends. At the same time there is the requirement to ease fulfillment of ‘on-demand’ orders concerning ever-expanding products.
Project Overview
A North American producer of goat feta, yogurt and ricotta sought aggressive expansion based on market demand for their goat cheese by rolling out new products and by optimizing product quality/value. The strategy used to achieve this included moving into a new facility, updating production methods and increasing plant space to accommodate new gourmet items and yogurt products. The expansion process identified the need to semi-automate – since it was a hand packing operation at the time. Semi-automation would help them meet their increased orders, thereby improving their delivery times and preserving product freshness. They were looking for case sealers that could not only be justified because they would increase production but could also be justified because they would ease case size changeover and offer flexible throughput of 5000 boxes per day to as little as 200 boxes per day, as needed.
The Customer Challenge
Gourmet feta and goat cheese products are typically contained within a plastic tub or similar container and, in this case, were thereafter being conveyed for packing. This facility was placing products into a cardboard outer shipper and sealing it for subsequent palletizing and transporting to major retailers. Previous to their Wexxar Bel machinery purchase, the outer shipper was formed and tape sealed by hand, causing a backlog that impacted delivery times.
The task of the packing line operator was to ensure that the equipment they selected ran with a high rate of efficiency to get enough products out the door each day and ensure freshness and quality. It was also critical that the machinery provided ease of changeover to erect and seal the appropriate case size for on-demand orders. They wanted to avoid pre-erecting and storing of multiple box sizes. Instead they would simply adjust the machine to suit the batch. By using a semi-automatic case former and semi-automatic case sealer, one operator was able to increase line productivity and free up plant space formerly used for pre-erecting cases.
The Wexxar Bel Solution
In the case of this dairy customer, Wexxar Bel specialists recommended the BEL 505g4 case former and BEL 150 case sealer, since this forming and sealing system was able to output cases at speeds of 15 cases per minute (cpm) and easily adjust to all of the plant’s box sizes. The machine could be changed over quickly, whenever they needed to do batch runs and it offered flexibility in terms of resizing and moving to a new yogurt line or soft cheese line.
The standard features of both the BEL 505g4 and BEL 150 systems provided a key combination of operator safety, delicate handling of cases and a seamless transfer of the product-filled box into the sealer. The ease of use for the operator ensured delicate products were handled with care and an aesthetic outer shipper was unspoiled. The tools free adjustment feature allowed for quick case size changeovers during daily operation.
Wexxar Bel systems come standard with high performance DEKKA brand tape heads, which provided a quality sealed case, both top and bottom. DEKKA tape heads are interchangeable and were able to be moved between machines, as needed. A heavy-duty drive system also ensured cases were squarely taped.
The BEL 505g4 and BEL 150 production benefits described in this article, along with the consistency of the formed package, were key determining factors for this dairy facility when selecting their machinery. Wexxar Bel was able to help them update their production methods to meet both their expansion and their quality/freshness goals.